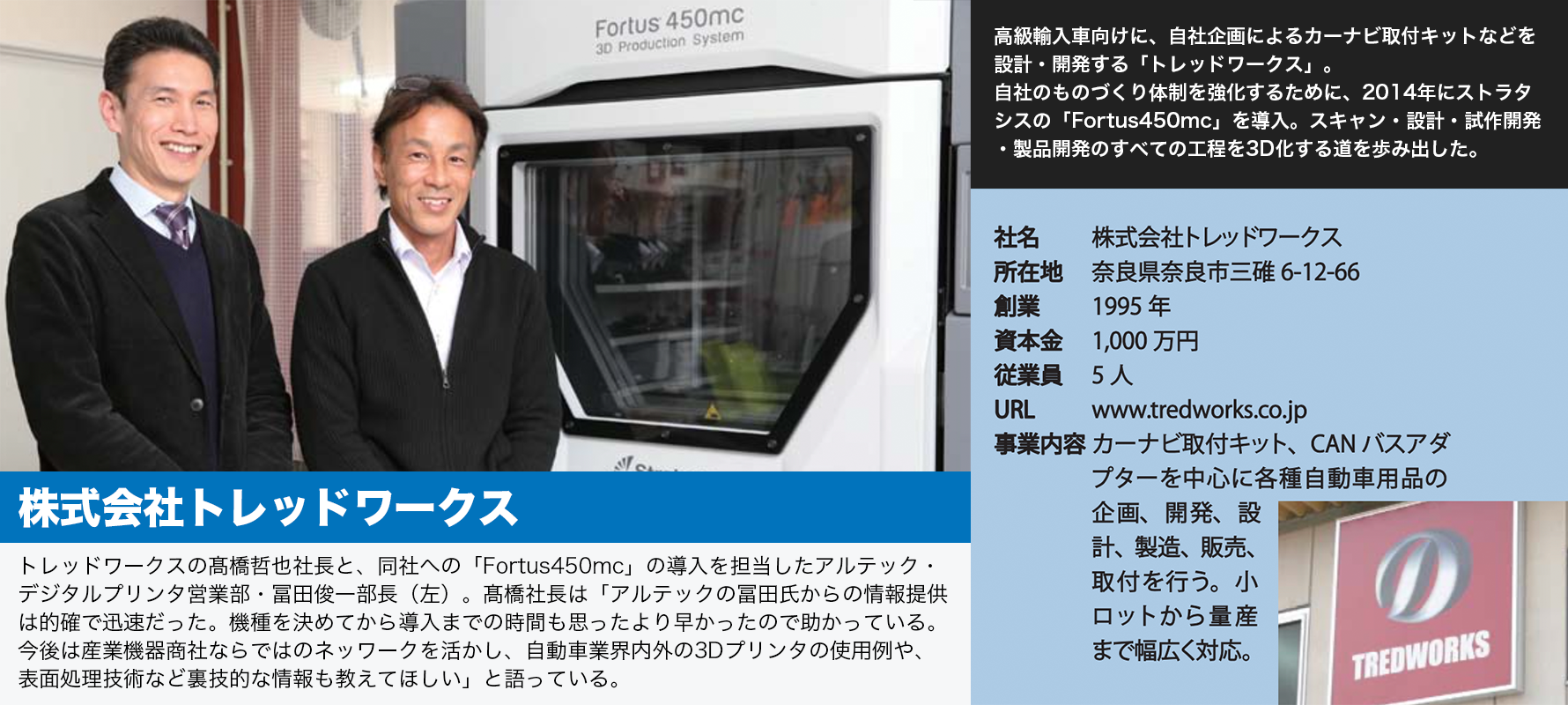
社名にこめた「3D」への期待 試作検討からカスタム品の直接製造まで(DDM)
高級輸入車向けに、自社企画によるカーナビ取材キットなどを設計・開発する「トレッドワークス」。
自社のものづくり体制を強化するために、2014年にStratasysの「Fortus450mc」を導入。
スキャン・設計・試作開発・製品開発のすべての工程を3D化する道を歩み出した。
社名にもこめた「3D」への期待。ものづくりプロセスの革新について聞いた。
お客様情報
社 名 : 株式会社トレッドワークス
所在地 : 奈良県奈良市三碓6-12-66
創 業 : 1995年
従 業 員 : 5名
事 業 内 容 : カーナビ取付キット、CANバスアダプターを中心に各種自動車用品の企画、開発、設計、製造、販売、取付を行う。小ロットから量産まで幅広く対応。
Webサイト : http://tredworks.co.jp/
この事例で登場した製品
Fortus450mc
汎用プラスチックからスーパーエンジニアリングプラスチックまで幅広い物性の材料に対応。試作から治工具・最終製品まで、強度のあるモデルを造形。
輸入車向けカーナビ取付キットなどをオリジナルに開発
貴社の事業をご紹介ください。
髙橋氏:1995年に大阪府東大阪市で創業しました。(前職は樹脂製品を扱う商社の営業マン。)
最初はベビーカーの部材供給などを中心とした商社としてスタートしたのですが、10年ほど前からものづくりにシフトし、カーナビ取付キットやブースト計ホルダーなど自動車インテリア部品の設計開発に軸足を置くようになりました。
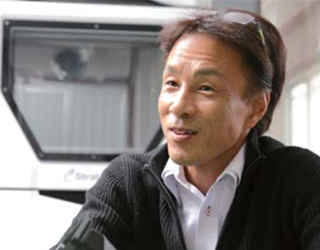
2011年には現在地に本社を移転、2013年からは3D設計・開発を意識して、社名も「TRE(イタリア語で3) + D (dimention) + WORKS(ものづくり)」を組み合わせた「トレッドワークス」に変更しました。
自動車部品といっても、当社の場合イタリア、イギリスなどのレアな輸入車がメインです。
こうした車に日本のカーナビなどを取り付けようとしても、寸法が合わないことが多い。エアコンの吹き出し口を改変したり、すきまが発生しないようなパネルを自作するとかしないといけない。
そうした特定車種向けにカスタマイズした部品を企画·設計しています。
取引先は輸入車ディーラーがほとんどですが、最近は当社が先んじて製品を企画し、それをディーラーに提案して製品化するということが増えています。
当社が意匠登録をもつ製品も少なくありません。
試作品検討にかかる時間が5分の1、コストが3分の1に削減
新社名が文字通り「3D」を意味しているわけですが、3Dプリンターを導入されたきっかけは何ですか。
髙橋氏:以前は、当社でざっくりと企画・設計を行い、試作品の製造や金型による量産は国内および中国の協力工場に外注していました。
しかしこれだと、どうしても時間がかかるし、試作のやり直しを繰り返せばそれだけコストもかかります。
それが気になって、途中でデザインを妥協せざるをえないときもありました。
そんなときに注目したのが、3Dプリンターです。
3DCADでデータを作成したら、翌日には試作品ができあがる。
それを実車に取り付け、嵌合チェックや走行テストをして異音の発生などをチェックします。
輸入車は国産車に比べると個体差が多いので、同じ車種でも微妙な変更が必要になるんですね。
3Dプリンターなら修整すべきところがあっても、すぐに直せます。
このラピッド・プロトタイピング(RP)によって全体の納期やコストはどれぐらい短縮されましたか。
髙橋氏:かつてデータを渡して試作品が届くまで1週間から2週間かかっていたものが、翌日にはできあがるわけですから、試作品の納期は最小でも5分の1にはなっています。
全体をとおしてコストも3分の1に低減していると思います。
小ロット品では、ABS樹脂を使いダイレクトに製品を製作
試作検討用途だけでなく、3Dプリンターからの造形をそのまま製品として採用することもあるのですか。いわゆるDDM(ダイレクト・デジタル・マニュファクチャリング)のとしての活用ですが。
髙橋氏:高橋氏売れ筋の車種向けに100個以上をつくるときは、試作→金型→量産というプロセスになります。しかし、それ以下の個数の場合はわざわざ金型を起こすのは手間もコストもかかります。
例えば「アストンマーティン」や「レンジローバー」などのプレミアム車向けキットは取付台数が限られるので、金型量産には向いていない。
しかしこうしたニッチな市場でこそ存在感を発揮したいというのが当社の戦略でもあリます。
当初は、小ロット製品については、NC切削機で自社加工しようと考えていました。
ところが、加工機のマーケットを調査していたところ、数年前から3Dプリンターの性能が格段に向上し、ABS樹脂などのリアルプラスチックを材料として使える製品も登場していることがわかりました。
特に、FDM(熱融解積層法)方式のプリンタなら、射出成形やNC加工で使用されるものと同じ、強度の高い安定したプラスチックで部品が作れるというところに注目しました。
私たちが扱う部材はほとんどがABS樹脂ですから、もしこれで寸法精度の高い立体が造形できるのなら、切削機を使わず、3Dプリンターでそのまま製品化できるのではないかと思いました。
高い精度、造形スピード、ABSマテリアルの耐熱性「Fortus450mc」選択の理由
ストラタシスの「Fortus450mc」を2014年11月に導入されているわけですが、この製品を選ばれたのはなぜですか。
髙橋氏:導入にあたっては厳密な各社製品のベンチマークを行なっています。
方式としては大きくインクジェット方式とFDM方式があり、それぞれ長短があります。
耐熱など車載条件に耐える材料が使えるということでFDMにすべきだとなりました。
たしかに市場にはもっと価格の安いFDM製品もあります。
ただ、造形をそのまま製品として使うためには、やはり一定の精度がないといけない。
低価格品はざっくりとしたデザイン検討などには使えても、製品レベルのものを作ることはできないとわかりました。
「Fortus450mc」ならそれが可能です。
実際に使われてみていかがでしょうか。
高宮克彦氏:実際のオペレーションを担当しています。
3Dプリンターの導入によって当社の開発スタイルがガラッと変わりました。
ある車種用のパーツを設計する場合、いつも実車が手元にあるわけではないですから、まず3Dスキャナーでダッシュボード周りをスキャンします(3Dプリンター導入を前提に3Dスキャナーを1年前に導入)。
スキャンデータの寸法に合わせて、パーツの3D設計を行い、それを3Dプリンターで造形します。
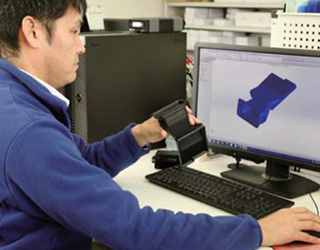
この一連の工程がすべて社内で行われるようになりました。
「Fortus450mc」は操作も簡単で、精度は高く、時間も短縮できる。ABS材料の耐熱性能も問題ない。
強度については、地元の工業試験所でテストしたデータをもっていますが、積層の方向によっては私たちのニーズに若干足りない場合もでてきますが、設計方法の工夫でカバーしています。
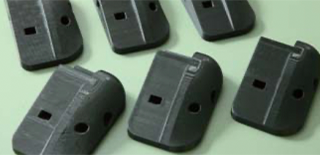
いずれにしても、私たち設計者のイメージがそのままの形になってすぐに出てくるところがいい。
DDMの場合、金型加工のところまで考えなくて済みますから、デザインの発想力、自由度が飛躍的に高まりました。
RPでも試作品がすぐに形になるというのは、設計者のモチベーションを維持していくうえでも大切な要素だと思います。
試作品が出てくるまでに1〜2週間かかっていたら、我々のテンションも途中で冷めてしまいますからね。
今後は3Dプリントサービスやワンオフ対応を強化
これからは、どのように活用範囲を広げていきたいですか。
髙橋氏:当面はABS樹脂ですが、今後はナイロンなど他の材料も使ってみたいと思います。パーツの2次加工などに使う治具の製造にも使えるんじゃないかと考えています。
3D設計・製造の一貫体制を自社に構築することで、近隣の同業者からのプロトタイプ開発を受託するなど、3Dプリントサービスを事業化することができるかもしれません。
私たちが対象としている車種では、メーカー純正のアクセサリーパーツや汎用品では満足されないユーザーが多いんです。
市場にはないパーツを手作りで作ってほしいという「ワンオフ対応」のニーズもかなりあります。これまではそうした注文は手間がかかるので断っていたんですが、「Fortus450mc」ならすぐに対応できるでしょう。
そういう方向への市場開拓も考えています。
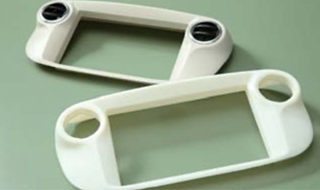
カーナビパネル
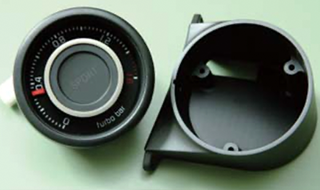
メーターパネルと独自設計の筐体
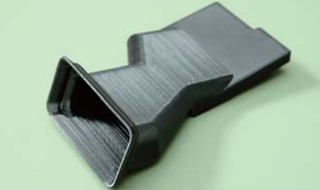
3Dプリンターで出力したエアコンダクト
ご協力ありがとうございました。
※上記コメントはお客様の個人のご意見・ご感想であり、当社の見解を示すものではありません。
この事例で登場した製品
Fortus450mc
汎用プラスチックからスーパーエンジニアリングプラスチックまで幅広い物性の材料に対応。試作から治工具・最終製品まで、強度のあるモデルを造形。